1. 1. Structure of electric wire
Wires are carriers for transmitting electrical signals and currents. They are mainly composed of insulation and wires. Wires of different specifications correspond to different insulation materials and copper wire structures. The evaluation parameters of the wire mainly include the copper wire diameter, number, insulation thickness and outer diameter of the conductor part. In order to reduce the degree of interference of different signals during transmission, twisted-pair wires and shielded wires are also used in automobiles. Due to the large amount of wires used on the vehicle, for the convenience of wiring harness production and after-sales maintenance of the whole vehicle, different colors are generally set for the insulation skin to distinguish them.
1. 2. Specifications of wires
The wires used in automobiles are mainly low-voltage wires. With the development of hybrid electric vehicles and pure electric vehicles, more and more high-voltage wire harnesses are used in automobiles. However, the author of this article mainly discusses low-voltage wires, with the current industry mainstream The wire specifications are Japanese standard wires and German standard wires.
2. Design and selection of automotive wires
2. 1. Wire ampacity
The ampacity of wires is a factor that must be considered in the design process, and the load current value of wires is specified in GB 4706. 1-2005. The current carrying capacity of the wire is related to the cross section of the wire, and also related to the material, type, wrapping method and ambient temperature of the wire. There are many influencing factors and the calculation is more complicated. The ampacity of various wires can usually be found in the manual.
Factors affecting the ampacity can be divided into internal factors and external factors. The properties of the wire itself are the internal factors that affect the current carrying capacity of the wire. Increasing the core area, using high-conductivity materials, using insulating materials with good high temperature resistance and thermal conductivity, and reducing contact resistance can all increase the current carrying capacity of the wire. External factors can increase the ampacity by increasing the wire layout gap and choosing a layout environment with a suitable temperature.
2. 2. Matching of wires, connectors and terminals
The matching of wires and connector terminals is mainly divided into matching of current carrying capacity and matching of mechanical crimping structure.
2. 2. 1. Matching of current carrying capacity of terminals and wires
The current carrying capacity of the terminals and wires should match to ensure that both the terminals and wires can meet the load requirements during use. In some cases, the allowable current value of the terminal is satisfied, but the allowable current value of the wire is exceeded, so special attention should be paid. The current carrying capacity of wires and terminals can be obtained by looking up tables and related information.
The allowable current value of the wire: the terminal material is brass, the current value when the terminal temperature is 120 ℃ (the heat-resistant temperature of the terminal) when energized; the heat-resistant copper alloy, the current value when the terminal temperature is 140 ℃ (the heat-resistant temperature of the terminal) value.
2. 2. 2. Matching of terminal and wire ampacity mechanical crimping part
In order to ensure the matching of the mechanical crimping structure, that is, the terminals must meet certain standards after crimping the wires. The influencing factors mainly include the following parts:
(1) When the wires are opened, it is necessary to ensure that the insulation and core of the wire harness are intact and undamaged. The typical structure after opening is shown in Figure.
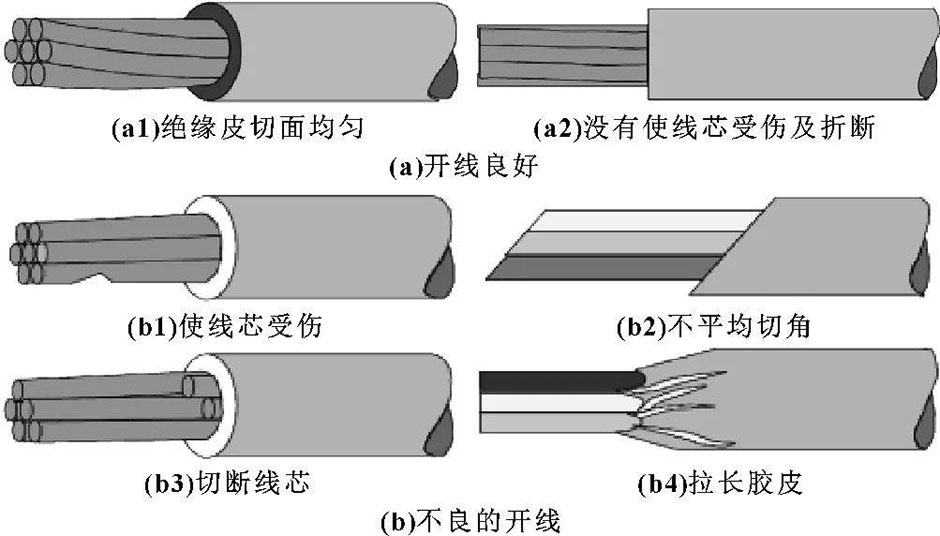
Post time: Dec-23-2022